Jumbo Bag Loading System
Jumbo bag loading system, also known as a big bag loading system or FIBC (Flexible Intermediate Bulk Container) loading system, is a mechanized solution designed to efficiently load and fill bulk bags with various types of dry, granular, or powdered materials. These systems are commonly used in industries such as agriculture, chemicals, minerals, food processing, and more, where large quantities of materials need to be transported and stored in bulk.
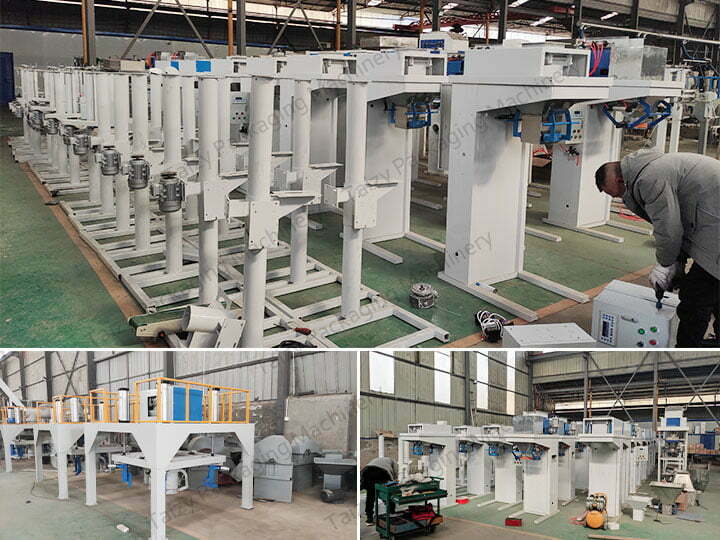
How a Jumbo Bag Loading System Typically Works?
Material Feeding
The raw material to be loaded into the bulk bags is usually stored in hoppers or silos. From there, the material is conveyed using conveyor belts, screw conveyors, or pneumatic systems to the loading station.
Bag Positioning
The bulk bag, which is a large, heavy-duty bag made of woven polypropylene or other durable materials, is positioned under the loading station. The bag is supported by a forklift or overhead hoist during filling.
Filling Mechanism
The filling mechanism is the core component of the loading system. It includes components such as filling spouts, flow control devices, and dust collection systems. The material flows from the conveying system into the bag through a filling spout, which is securely attached to the bag’s inlet. Flow control devices ensure uniform filling and prevent overfilling, ensuring the bag’s stability and structural integrity.
Dust Collection
Since many materials can generate dust during the loading process, a dust collection system is often integrated into the loading system. This helps maintain a clean and safe working environment and prevents the escape of fine particles into the air.
Weighing and Monitoring
Depending on the application, the system might include a weighing mechanism to accurately measure the quantity of material being loaded into the bag. This is important for inventory management, quality control, and compliance purposes.
Closure and Removal
Once the bag is filled to the desired weight or volume, the filling spout is closed and sealed to prevent any spillage. The bag is then detached from the loading system and either sealed using integral ties or other closure mechanisms.
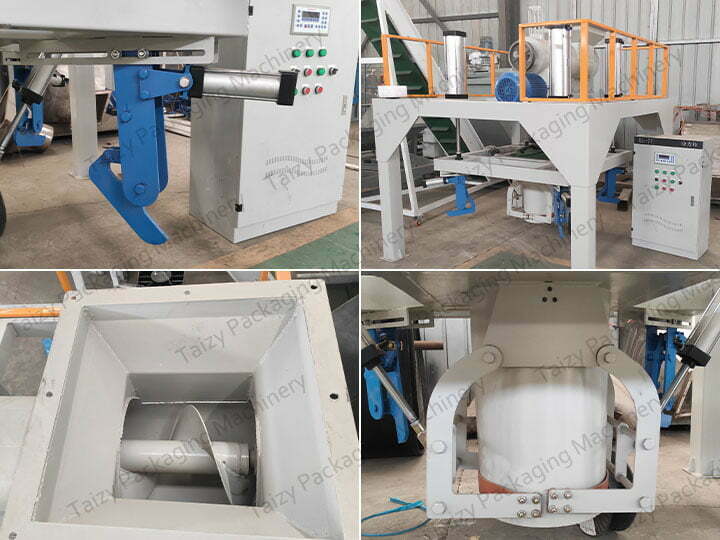
Key Advantages of Using a Jumbo Bag Loading System
- Efficiency: These systems can handle large quantities of materials quickly and efficiently, reducing the labor required for manual bag filling.
- Reduced Labor Costs: Automation of the filling process minimizes the need for manual intervention, leading to cost savings in labor.
- Minimized Dust Emissions: The dust collection system helps maintain a clean and safe working environment by capturing and containing airborne particles.
- Accurate Weighing: Integrated weighing mechanisms ensure accurate measurement of materials loaded into each bag.
- Consistency: Automated systems provide consistent filling, reducing the likelihood of errors and ensuring uniform bag weights.
When selecting a jumbo bag loading system, it’s important to consider factors such as the type of material being handled, the required filling rate, the accuracy of weighing, and any specific safety or regulatory requirements in your industry. These systems are often customizable to suit the unique needs of different industries and applications.