Vacuum capping machine sold to Vietnam
A customer from Vietnam
The customer has already bought three times machines from our company before, which are a chicken cutter, meat slicer, and frying pan. This time the customer originally wanted a bottle capping machine and a bottle cleaning machine. Our business manager explained to the customer that bottle packaging is divided into the following steps: bottle cleaning, bottle unscrambling, filling, capping, labeling, and coding. The three key steps are filling, capping, and labeling. Then the customer showed interest in the labeling process, so our manager introduced our labeling machine to him.
Because the filling machine the customer bought before was semi-automatic, he needed to match the semi-automatic capping machine. Considering that he was running a food factory and had high requirements for the corresponding packaging of food, he recommended this semi-automatic vacuum capping machine, which is beneficial to the storage of food. After sending the working video of the vacuum capping machine to the customer, the customer was satisfied with it and said he also needed our automatic labeling machine.
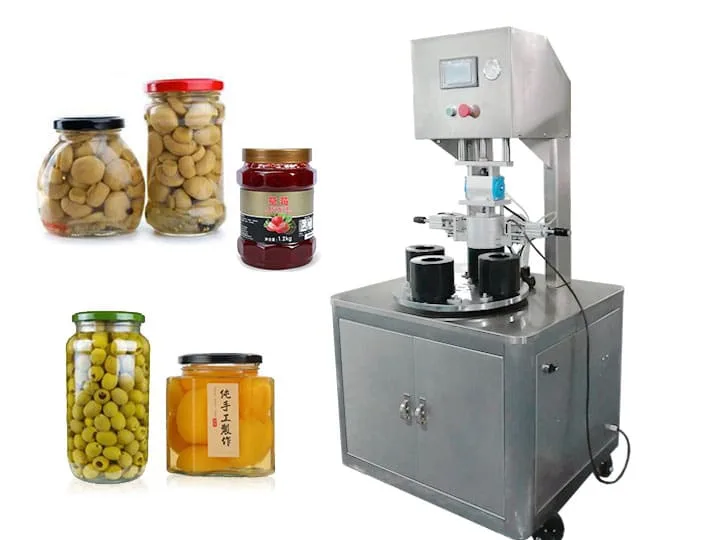
Packing and transportation of vacuum capping machine
After confirming the delivery time and address with the customer, we contacted the factory to arrange the delivery immediately. Taizy company has more than ten years of experience in food packaging machinery and equipment. Our products are sold all over the world, including Pakistan, Sri Lanka, Vietnam, Nigeria, and other countries. Our company has formed a complete system from packaging to transportation. We devote ourselves to avoiding the extra loss of transportation to the maximum extent.
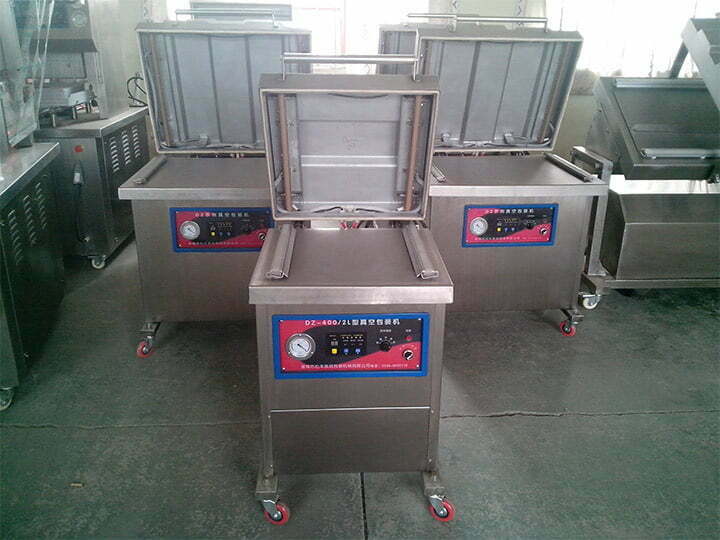
The advantages of vacuum capping
- Firstly, zero loss rate. We know that the vacuum capping machine fixed bottle is achieved through the cylinder drive. The cylinder drive with an intelligent design adjustment process is very accurate, not because of errors in operation and damage to the bottle
- Secondly, the working environment is clean and tidy. The machine as a whole is driven by the power of an air compression cylinder to complete the work, with no traditional mechanical oil, to ensure maximum food hygiene
- Thirdly, low energy consumption and good adaptability. The machine forms a completely airtight environment during the capping process to achieve the highest vacuum level and low energy consumption. A machine can adapt to different shapes of bottles by changing molds.